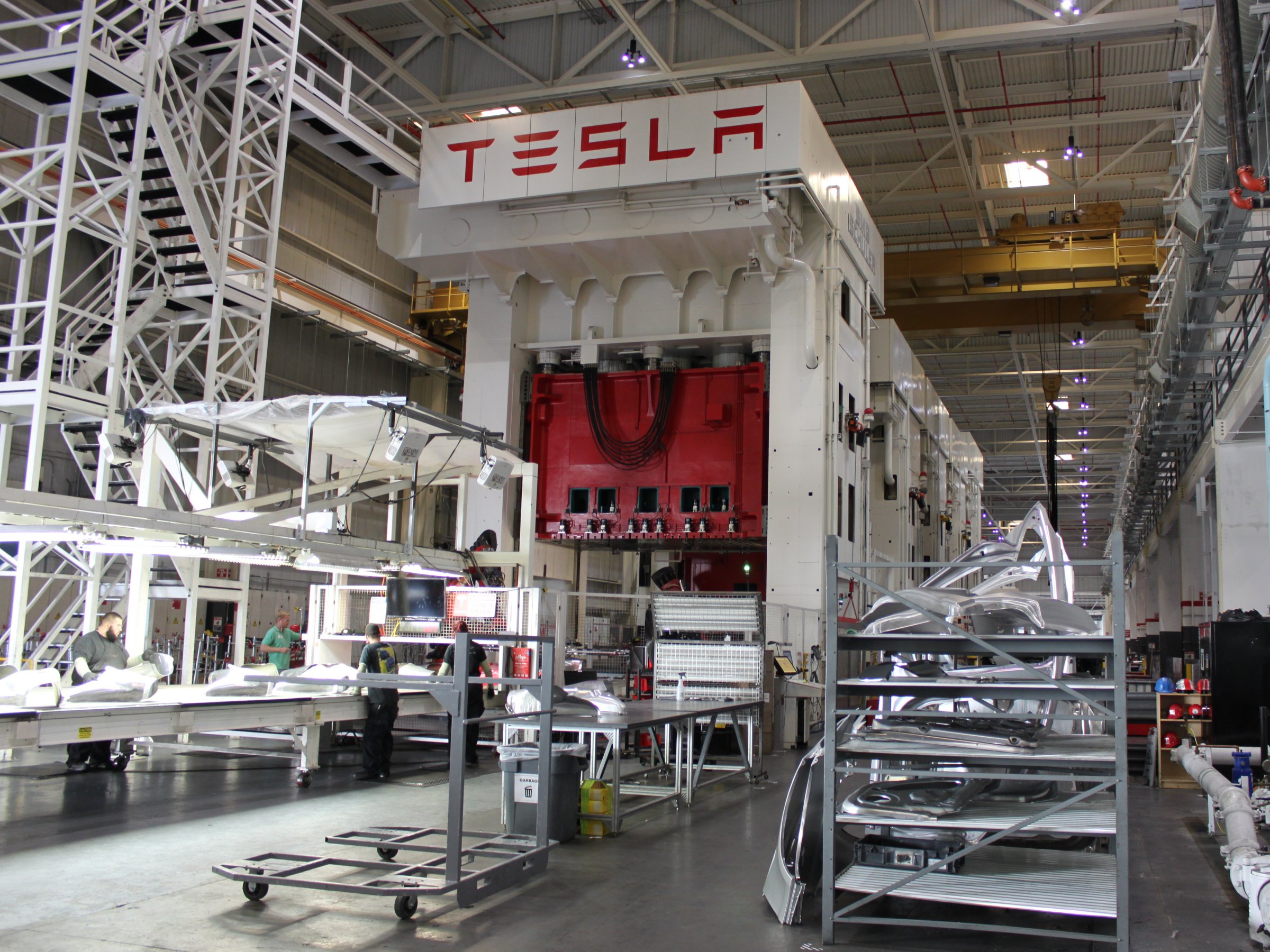
Inside the Tesla factory. Benjamin Zhang/Business Insider
Tesla’s factory in California has a theoretical manufacturing capacity of 500,000 annually. Toyota and GM built almost that many there in 2006.
- Tesla is struggling to hit its manufacturing targets for the Model 3.
- Its factory produced close to 450,000 vehicles annually when it was run by GM and Toyota.
- Tesla bought the plant for $42 million in a 2010 — a massive bargain.
Tesla is deep in what CEO Elon Musk called “production hell” on its new and hotly anticipated Model 3.
The vehicle is currently selling for $44,000, but base-priced at $35,000 for a version that doesn’t have all-wheel-drive and premium appointments. Tesla has about 500,000 pre-order in the books, at $1,000 a pop, but production is troubled.
Tesla said it would build 1,500 Model 3s in September, but in the entire third-quarter, it managed only 260 vehicles. It’s unlikely that 20,000 Model 3s will roll off the assembly line in December, as Musk predicted.
Meanwhile, Tesla has a good chance of building about 100,000 Model S and Model X luxury vehicles in 2017 — more than ever before.
Interestingly, Tesla’s factory in Fremont, CA, has a theoretical manufacturing capacity of 500,000 vehicles annually. That’s because back in the 1980s, it was called New United Motor Manufacturing, Inc. (NUMMI) and was run as a partnership between General Motors and Toyota.
If Tesla has an Achilles’ heel, it’s that it can’t build cars with the same relative ease as other major automakers. The contrast between what was happening at NUMMI in the ’80s and what’s happening now highlights this problem.
Here’s a photo of NUMMI from back in the day. It looks very much like an old-school car factory.
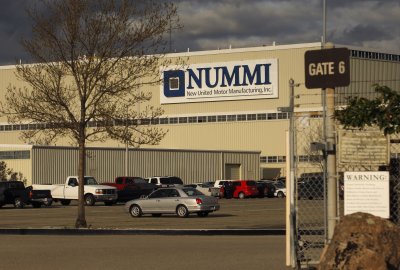
Looks can be deceiving. NUMMI was perhaps the most important plant in automotive history, after Ford’s legendary River Rouge factory.
It actually dated to the early 1960s, when GM opened it as Fremont Assembly. By the mid-1980s, it had been revamped through a joint venture between GM and Toyota. In fact, NUMMI was essentially a separate manufacturing company.
The goal for GM, in particular, was ambitious: learn the by-then famous Toyota production method, which combined continuous improvement of manufacturing (the Japanese concept of “kaizen”) with so-called “lean” or “just in time” production.
Follow us on Twitter for more Logistics News
The idea was that much greater efficiency, cost savings, and quality control could be achieved if parts inventories were kept light; materials would arrive “just in time” at the assembly lines.
Sounds good, but it required a very high level of supply chain management and workforce training. It’s the opposite of “vertical integration,” the system of doing everything in one place that defined the auto industry before Toyota disrupted the paradigm.
Ironically, Tesla CEO Elon Musk now wants to take Tesla’s production back to the vertical model.
NUMMI was closed down in 2010.
And here’s the same factory, rebranded by Tesla.
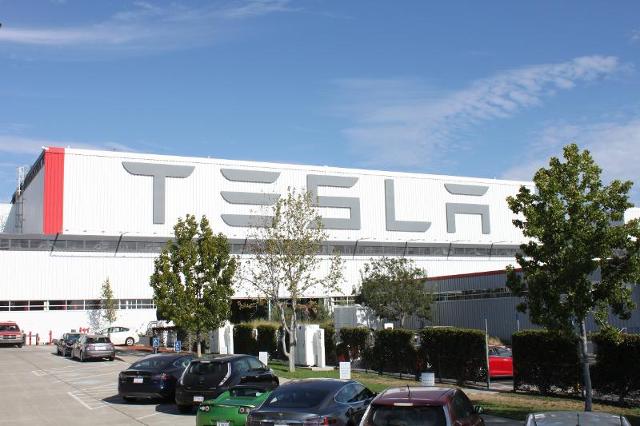
I’ve visited the Fremont, CA plant and there’s no doubt about it — it’s a cool place.
But the contrast between what two big car companies were able to do with the factory in its heyday and Tesla in 2017 is vivid. With an annual manufacturing capacity of 500,000, NUMMI topped out at about 430,000 in 2006, before GM and Toyota, shuttered the plant. (The numbers come from IHS Markit, cited by Bloomberg.)
Follow us on Facebook for more Logistics News
Tesla projected that it would achieve 500,000 in annual production in 2018, but that goal now seems precarious.
It appears that the company has maxed out manufacturing for its Model S sedan and Model X SUV at 100,000 units yearly. That means the factory formerly known as NUMMI needs to produce as many Model 3 mass-market vehicles for Tesla as it once did Toyota Matrixes and Pontiac Vibes for Toyota and GM.
Tesla acquired NUMMI for a fire-sale price after GM’s bankruptcy: $42 million. An auto factory can cost over a billion dollars to construct new — something Tesla needs to keep in mind as it marches towards Musk’s even more bold goal of a million vehicles annually by 2020.
Culled from BI